From Consumer Electronics to Aerospace, a design service helps you prepare your product for mass production efficiently. With their help, you’ll create something that’s optimized in terms of cost, quality and time to market.
So many processes contribute to your product’s success, from design to mass production, that it’s easy to lose sight of a detail or two. Here’s how to know when it’s time to take the final step in your product’s journey from design to mass production.
How to Know You’re Ready for Mass Production ?
These key milestones in your product development journey indicate that you’re ready for mass production :
- Do you have a product that’s ready for market ? Without this, mass production logically can’t begin. To ensure the design and manufacturing process produces the best possible product, it pays to partner with an EMS provider that’s also a Design for Excellence (DfX) expert. Read more on how design and DfX work to bring your product to market, in this blog post.
- A partnership with an Electronic Manufacturing Services (EMS) provider : ideally, your EMS partner would work with you from the beginning, as this is the best way to safeguard quality and general process optimization. But if you’ve completed your design, prototyping and manufacturing processes internally already, bringing an EMS partner on board now will be necessary. For tips on what to look for in an EMS provider, and to learn more on how they can help you improve product value, read our essential guide.
- Does your EMS partner have the capacity to produce on a mass scale ? Finding the right partner is essential to ensure mass production is completed successfully. It’s critical to ensure your provider has the capacity to produce at scale. Confirm that your intended EMS provider has the manufacturing capabilities and manpower to see mass production through to a high standard, and to mitigate potential challenges. Key questions include:
- Do they have multiple factory locations ?
- Does each plant have a full set-up, with all services they need to realize mass production ?
- What team oversees the process from design to mass production? What are their roles, expertise or skills? How does this change at each stage ?
- Ability to commit to minimum number of products : how many units you’ll need to mass-produce for the project to be economically viable is determined by your industry. For consumer electronics, this may be 50,000–100,000 units, while for defense and aerospace it may mean 50–150 units per project. Confirm that your EMS provider can manufacture the minimum number you need, in terms of both labor and physical resources, and capacity to meet your desired deadlines.
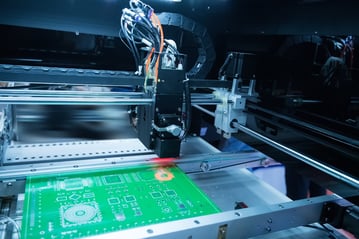
How Design for Excellence adds value to mass production ?
A number of routine challenges have to be addressed at each stage of the design process before the manufacturing and mass production can begin. Partnering with an EMS company that specializes in Design for Excellence (DfX) methods, means your product is optimized through critical review at each stage of its lifecycle.
DfX is your guarantee against unusable products, inflated costs and unnecessary delays. Partnering with a DfX EMS company from design to mass production reduces time to market, ensures efficiency and lowers risk of failure during production and assembly.
Our recommendation? Bring your EMS partner on board sooner, rather than later, for the greatest benefits. Contact Asteelflash and get a quote on your latest project. We have seventeen plants worldwide, each with full mass production capability across multiple industries. Let us know what your goals are and we’ll help achieve them, quality guaranteed.